Jazzros 3D Custom Fit Technology: Personalization at Scale
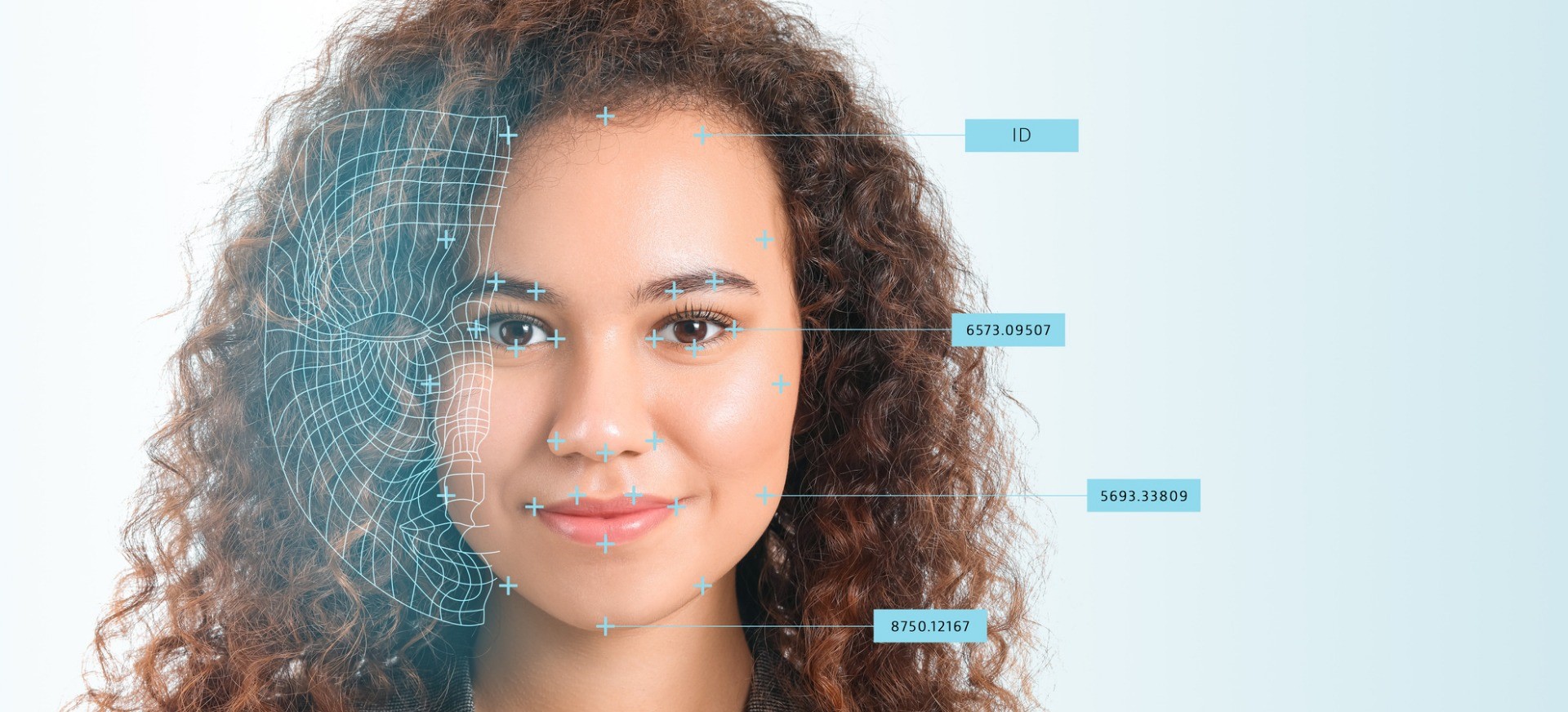
Introduction
At Jazzros, we believe that mass customization is an integral part of Industry 4.0. Personalized products that offer superior quality, fit, and comfort can be manufactured faster, for less money. We have dedicated our resources and expertise to develop an innovative solution that can accelerate and automate the design, modeling, and production processes to turn 3D measurements into 3D custom fitting products.
About Jazzros
Founded in 2009, Jazzros is a software engineering company that builds complex software solutions for Industry 4.0. The team at Jazzros uses its extensive experience in Computer Vision, 3D Scanning & Reconstruction, CAD, Parametric Design, and Additive Manufacturing technologies to develop innovative products and help clients solve their complex technological challenges.
Mass-customization technology
Harvard Business Review outlines that customized additive manufacturing can be a “full-fledged competitive weapon” to hold on to market leadership, move to the top, or diversify to new industries. The technology has significant potential and far-reaching applications that will dominate the future of manufacturing.
The complexity of technology and high-quality additive manufacturing prices have kept out smaller companies and entrepreneurs out of the mass-customization market. Now that industrial 3D printing has become significantly cheaper, even designers without experience in 3D modeling can use innovative software to model and create unique 3D custom-fit products.
The technologies behind the mass-customization process can be divided into the following parts:
3D Scanning & Reconstruction algorithms
Custom 3D products are created from input data that can be collected using different devices. Modern Photogrammetry and Computer Vision technologies can process photographs taken on a smartphone by an average consumer, diminishing barriers for custom mass-market manufacturing. The technology is used to obtain 3D coordinates of the target surface and reconstructs the object digitally.
Parametric modeling
The parametric modeling process uses algorithms to generate a complete 3D model of a custom object from several input parameters. By mathematically defining relationships between parameters, core design can be modified and iterated to reflect personalized data. Parametric design is a vital part of 3D custom-fit products as the algorithm defines and determines the design and specifications of the final product.
Unlike the traditional parametric CAD software that an operator needs to adjust manually, our modeling solution was built to facilitate automation. The algorithm can make adjustments without the need for continuous human input. The time from input to output is reduced significantly by letting computers do the job, making the process much more efficient and cost-effective.
Adjustment algorithms
To ensure a perfect fit or application of a 3D custom-fit product, the parametric modeling algorithms need to be adjusted to establish and map relations between 3D scans and parameters.
Engineers can make changes directly based on applicable data, knowledge, or experience. These changes can be automated by writing and implementing mapping functions. Taking it a step further, machine learning with enough training sample sets can output outstanding results with precise adjustments to the model. A combination of the three methods helps to generate the best results in practice.
3D Custom-fit applications
The technologies that make mass customization possible can be applied to a diverse range of products. In the last few years, 3D custom-fit solutions started to appear on the market. They began capturing market share with new exciting applications and features by addressing the inefficiency of traditional production.
The standard fixed sizes (S, M, L, XL, etc.) are based on outdated production and stock management processes. To maintain a wide variety of sizes consumers might order, a manufacturer needs to manufacture and store a lot of inventory, which requires a lot of time and resources. To minimize expenses, sellers usually restrict the number of sizes, which decreases the likelihood of consumers finding the right fitting product.
To provide some degree of adjustment between sizes, traditional manufacturers often implement additional structures and components for users to modify for a fit they want. The extra weight, materials, and assembly increase costs and decrease the longevity of said products.
3D custom-fit technology eliminates these problems by creating perfectly fitting products on demand. No unnecessary components increase the durability of the products, and flexible sizing solves inventory problems. Customers receive what they want when they want.
Our experience
The team at Jazzros relied on their experience developing Industry 4.0, Computer Vision, and 3D data processing solutions to build a product that covers all stages of a parametric creation process, from 3D scanning and generating a model from parameters to getting a G-code file ready for 3D printing.
Figure 1: Renders of insole layers at various printing stages powered Jazzros technology
The cloud-based modeling software developed by Jazzros has surface generation functionality that is 47 times faster than a conventional modeler, Rhinoceros, with the same accuracy of 0.2-0.3 mm. The solution generates a polygonal model displayed in a browser and a G-code file for 3D printing in a matter of seconds.
Figure 2: 3D printed insoles by Jazzros
The out-of-the-box product not only significantly improves production capacity but cost efficiency for additive manufacturing applications by speeding up the modeling process through all stages and reducing the cost of hardware and software by deploying it in the cloud.
Comparable industry examples
Given the project’s speed and versatility, it can be applied to various parametric additive manufacturing tasks. Similar software is used to create unique products in many industries, from fashion and transportation to medicine and aerospace:
Hearing
By scanning the ear canal to create a comprehensive 3D model, a range of personalized hearing aids, earphones, and noise protection devices were made possible. The perfect fit not only improves comfort but the quality of sound and noise isolation for professional, consumer, and industrial applications alike.
Sonova, for example, has been among the first companies to tailor the shape of the hearing aid shell to the wearer's individual ear canal and degree of hearing loss.
Figure 3: 3D printing technology for improved hearing by Sonova
Protection
When it comes to the human body, the better the fit, the better the protection. 3D custom-fit has been successfully applied to helmets that are safer than traditional foam alternatives. 3D printed casts by Xkelet protect and speed up the healing of bone fractures and breaks.
Figure 4: 3D printed casts by Xkelet
Personalized face masks like that developed by WASP use a 3D scan of the wearer to create a tailored mask with a replaceable filter to protect against viruses and bacteria.
Figure 5: Custom 3D printed Mask by WASP
Eyewear
Olympic swimming athletes are already using custom 3D printed goggles by the THEMAGIC5 that provide superior fit and reliability. Comfortable custom glasses and protective eyewear are no longer prohibitively expensive with 3D printed features such as screwless hinges that improve longevity and durability.
Figure 6: Custom Fitted goggles by TheMagic5
Footwear
Personalized footwear helps people reach new heights in sport, improve comfort for those on their feet all day, and help those with foot ailments. Customization can even turn a pair of ill-fitting shoes into comfortable ones with custom insoles like those by Leading Foot Technology.
Figure 7: Insoles by LFT
Summary
Many companies are intrigued by the potential of mass customization in additive manufacturing but are still wary of the risks. Large-scale commercial production of custom-fit products can alter the competitive landscape before the market becomes saturated. Now is the time to move beyond outdated manufacturing techniques and make the best of available technology.
To enable comments sign up for a Disqus account and enter your Disqus shortname in the Articulate node settings.